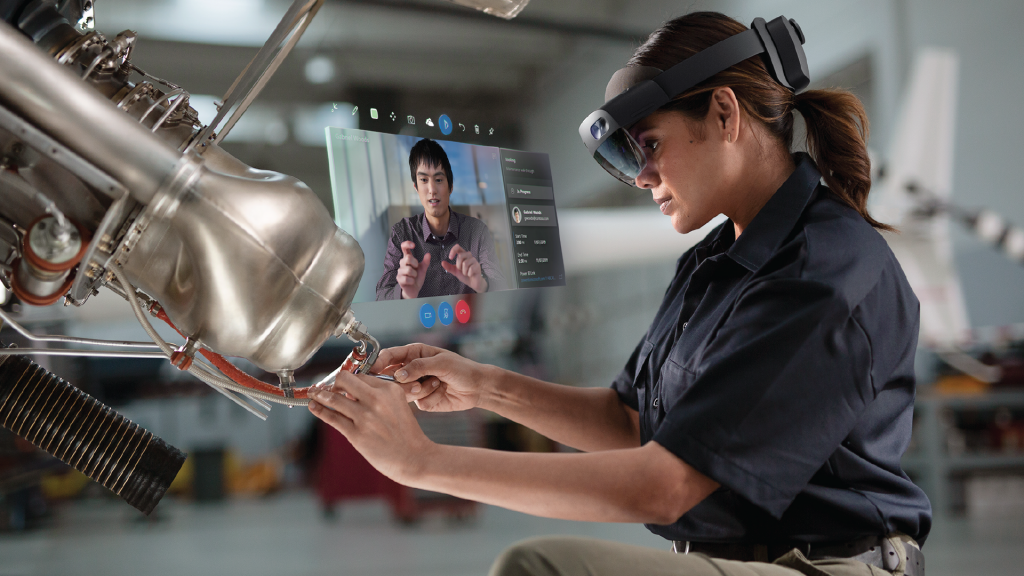
Workforce transformation in the intelligent manufacturing era
While technology is radically changing how we innovate, make products, deliver services, and explore new business models, it’s no surprise that people are at the core of digital transformation. Nowhere is this more apparent than in the manufacturing industry, where leaders who are embracing digital transformation are faced with addressing a significant skills gap and an aging workforce. The generation now entering the workforce isn’t pursuing careers in manufacturing as previous generations did, and even the most skilled existing manufacturing employees need new tech skills to remain competitive in the job market.
Embracing advanced technology can enable workforce transformation by closing the skills gap, advancing modern roles, reskilling to accelerate a data-driven culture, and empowering the first-line worker. These imperatives are top-of-mind for every leader in the manufacturing industry.
Closing the skills gap
To attract new workers to jobs in manufacturing, a modern, technologically-advanced workplace is critical. Younger employees are eager to embrace cutting-edge technologies such as mixed reality. Beyond the “cool factor,” mixed reality enables inexperienced workers to learn more quickly by simulating on-the-job experiences. Companies like Honeywell are leveraging immersive training to educate employees. When this model is leveraged, employees retain information much longer – in most cases up to 80 percent of information is retained after three months, compared to 20-30 percent with passive learning.
Advancing modern roles for the modern workplace
New technologies, combined with things like autonomous systems and collaborative robots, can also keep aging workers on the job longer as their expertise can now be made available virtually wherever it is needed. Manufacturers should also start planning today for the new digital jobs of tomorrow. This is about thinking beyond coding and computer science roles to focus on AI, data science, design, and other growing fields.
Reskilling to accelerate a data-driven culture
To support our current employees’ relevance in the digital workplace, we need to re-think education, industry training, and on-the-job readiness activities. Microsoft recently launched our AI Business School that helps companies learn how to strategically apply AI to transform their business and their culture. Tools like Microsoft 365 accelerate a modern, intelligent workplace that immerses employees in digital technologies and built-in AI capabilities in our software. Manufacturers like Goodyear report that these kind of tools enable their existing staff to modernize their factories and workplaces, optimizing efficiencies to create better experiences for customers.
Empowering the first-line worker
According to Forbes Insights, companies can realize an 88 percent bump in operational efficiency and cost savings by digitally equipping first-line workers. Just look at the work Chevron is doing with Dynamics 365 Remote Assist and HoloLens. By deploying the Remote Assist app, Chevron’s distributed workforce can assist each other remotely, drastically cutting travel costs. Equipment inspections that used to require monthly flights from the Houston headquarters to a facility in Singapore can now be completed remotely, using Dynamics 365 Remote Assist. Technology is enabling a 10,000 mile journey to become immediate – issues can be identified and approvals can be made just in time.
Cultural transformation is at the heart of any digital transformation, and manufacturing is no exception. The companies that work to create cultures that enable change are going to differentiate themselves in their respective markets, for sure, and Microsoft is excited to help them accelerate!
For more insights on Digital Transformation, find me on Twitter and LinkedIn.
Download the e-book The Future Computed: AI for Manufacturing.